Resistivity
Differences in Resistivity values provide practical means for
NDT inspection and process control. Rapid and accurate
measurements of electrical resistivity can be obtained with PAC products
yielding either bulk or surface characteristics of the component or
material being tested.
Applications
The
M100A
Metal
Inspector
Simple and Effective Nondestructive
Testing for Q.C. and Manufacturing of Metals
Materials Characterization
Because
resistivity values for most metals are already
well established, you can use the NDT
Automation
M100A
Metal Inspector to rapidly identify a metal through its
resistivity “value”. Surface Conditions, such
as oxides or paint, usually do not affect the accuracy of the test because
the system acclimates itself to the base material. Technically skilled
people or intermediate calculations are not needed. You receive an
accurate
readout
in <1 second.
Fault Detection
The
M100A
Metal Inspector can also detect cracks or pockets in metals by the
increase they cause in the measured voltage. This increase is due to the
lengthening of the apparent current path. If the probes are applied on the
side of the fault, the increase is very dramatic. But the
M100A
is so sensitive and accurate that faults on the inside of closed areas,
such as pipes, can often be detected and measured by the probes on the
outside surface.
Case Hardening
The
M100A
Metal Inspector makes it possible for the first time to quickly measure
the state of transformation of material undergoing case hardening. In the
martensitic transformation, for example, the
case hardened surface has a large resistivity
compared to the soft core or the original material. For typical steels,
studies have shown that there is a direct proportional relationship of the
hardened material.
Welding
The
M100A
Metal Inspector can give you a good indication of the strength of a spot
or laser weld. NDT Automation has correlated
weld strength with the voltage reduction measured across
resistance spot and various other welds. The
underlying principle: the larger the weld nugget and the cross-sectional
area of the weld, the lower the voltage measured, indicating greater weld
penetration.
The
M100A
Metal
Inspector at Work
Easy
To Operate
The
M100A
Metal Inspector is designed for easy use. Simply select the mode of
operation (sheet or block), set the dial for thickness or relative
percentage value, set your threshold (optional), place the probe on the
material and push the button. Readouts are in micro-ohms
centimeters, and require minimal operator
interpretation. Thickness readouts are in millimetres or inches. The
entire setup process can be learned quickly, and is normally performed in
less than a minute. Subsequent readings take less than a second.
Applications:
Alloy Sorting, Laser/Spot Weld Quality Control, Thickness Measurement,
Case Hardening.
The
M100A
using resistivity to
quickly and accurately help you measure brazing quality in pipe
joints and fittings.
The nondestructive
resistivity testing technique can be used to determine the
uniformity of filler materials and helps detect areas where voids
may exist. |
The
M100A
using resistivity to
quickly and accurately measure the thickness of conductive coatings
sprayed on metal to metal and metal to non-metal surfaces. This
nondestructive testing technique also
helps you locate and “size-up” areas where hidden voids, inclusions,
or poor adhesion conditions may exists. |
The
M100A
using resistivity to help
determine the case depth and hardness of metal.
It pulses a rapidly reversing direct current into metal through a 4-
point probe, and measures the metal’s resistance to the current
flow. Greater Case Depth = Higher Readings. |
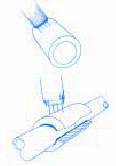 |
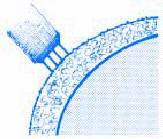 |
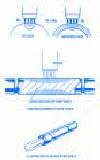 |